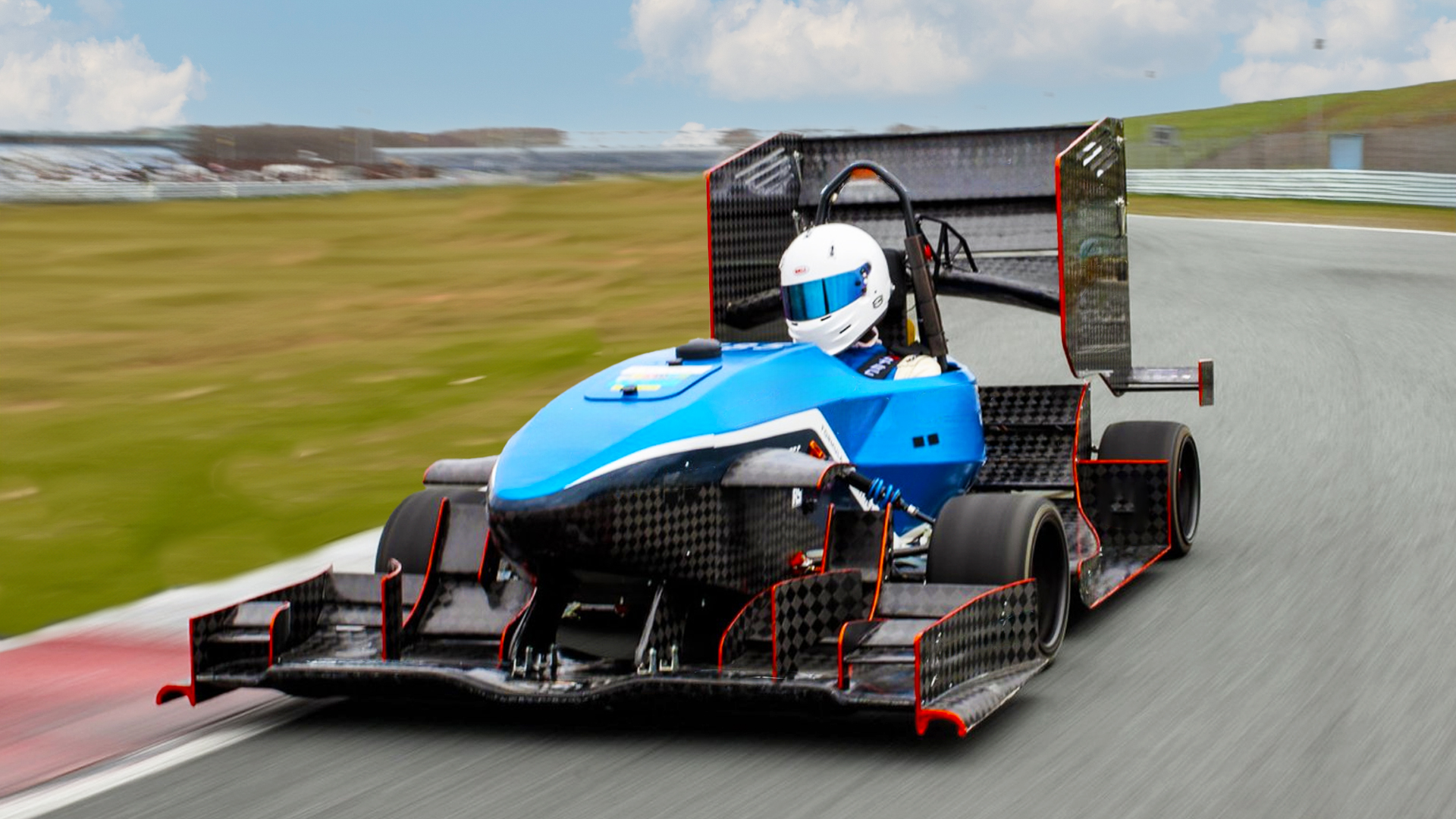
When people think of motorsport innovation, Formula 1 often comes to mind. Yet, groups of students around the world are designing and building cars that, in certain ways, rival or even surpass F1 in terms of innovation. These student-built vehicles may look like small race cars with exaggerated wings, but they pack incredible technology, speed, and precision.
The Formula Student Competition
Formula Student is a global motorsport engineering competition with events across countries like the UK, US, Germany, and Japan. Germany’s event is particularly prestigious, attracting top-tier teams. Oxford Brookes University is one of the institutions with a Formula Student team, and their work showcases the engineering skill required to compete in such an arena. The UK competition, held at Silverstone, involves both static and dynamic events, testing everything from the cars’ design and budget use to real-time performance on the track.
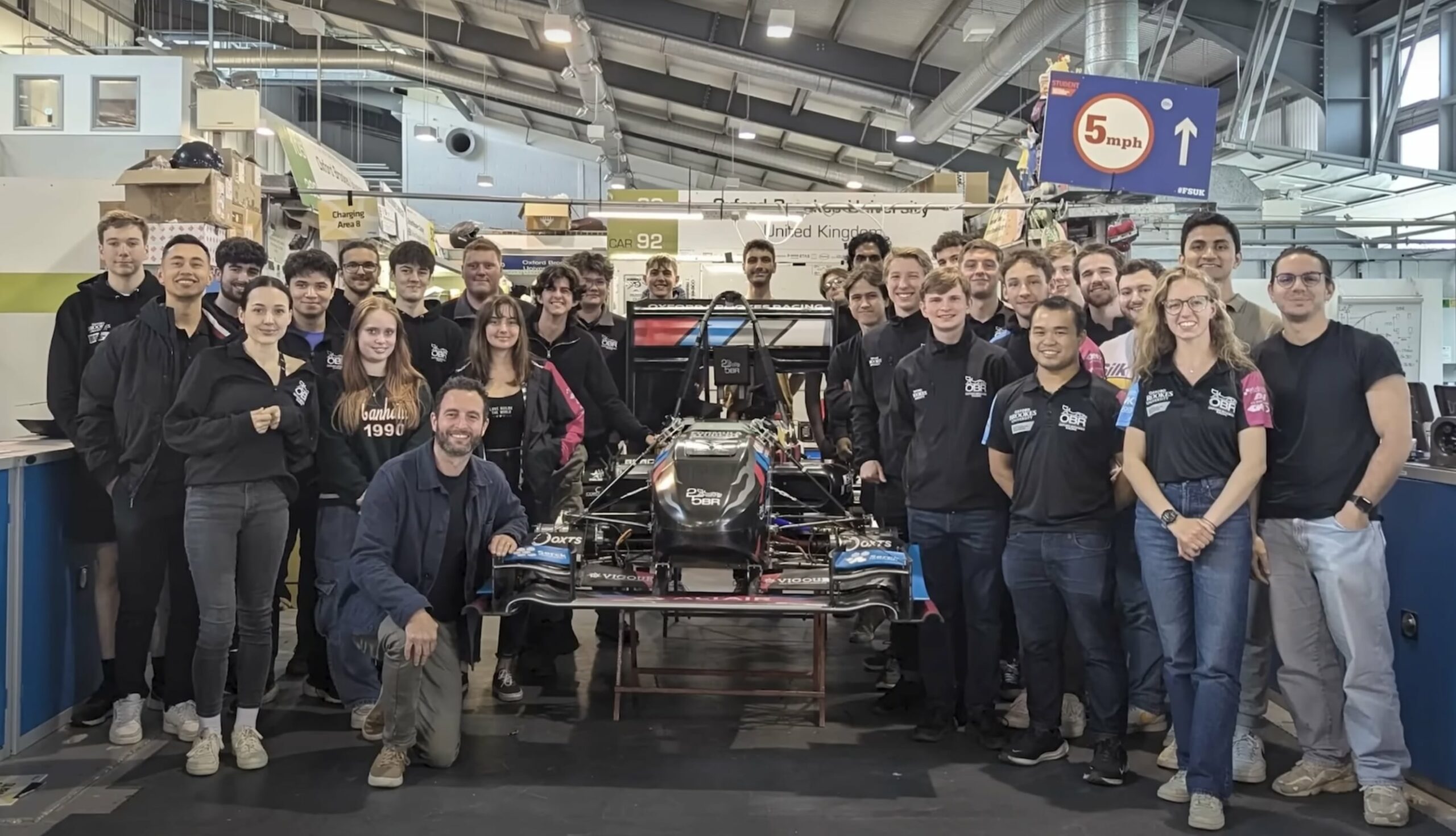
The Engineering Mastery Behind the Oxford Brookes Car
The Oxford Brookes car weighs just 244 kg – less than a third of an F1 car’s weight. This lightweight design allows for impressive handling on twisty circuits. At the heart of its performance are four independent electric motors, each housed within a wheel, making the car all-wheel drive and enabling precise control over each wheel.
Powertrain and Torque Vectoring
The four-motor setup gives the car incredible agility, thanks to torque vectoring, a technique allowing each wheel’s power to be controlled independently. Similar to how a tank operates, the car can accelerate or decelerate wheels on either side to make tight turns. This precision means the car maintains grip and control through every corner, utilizing every ounce of traction available.
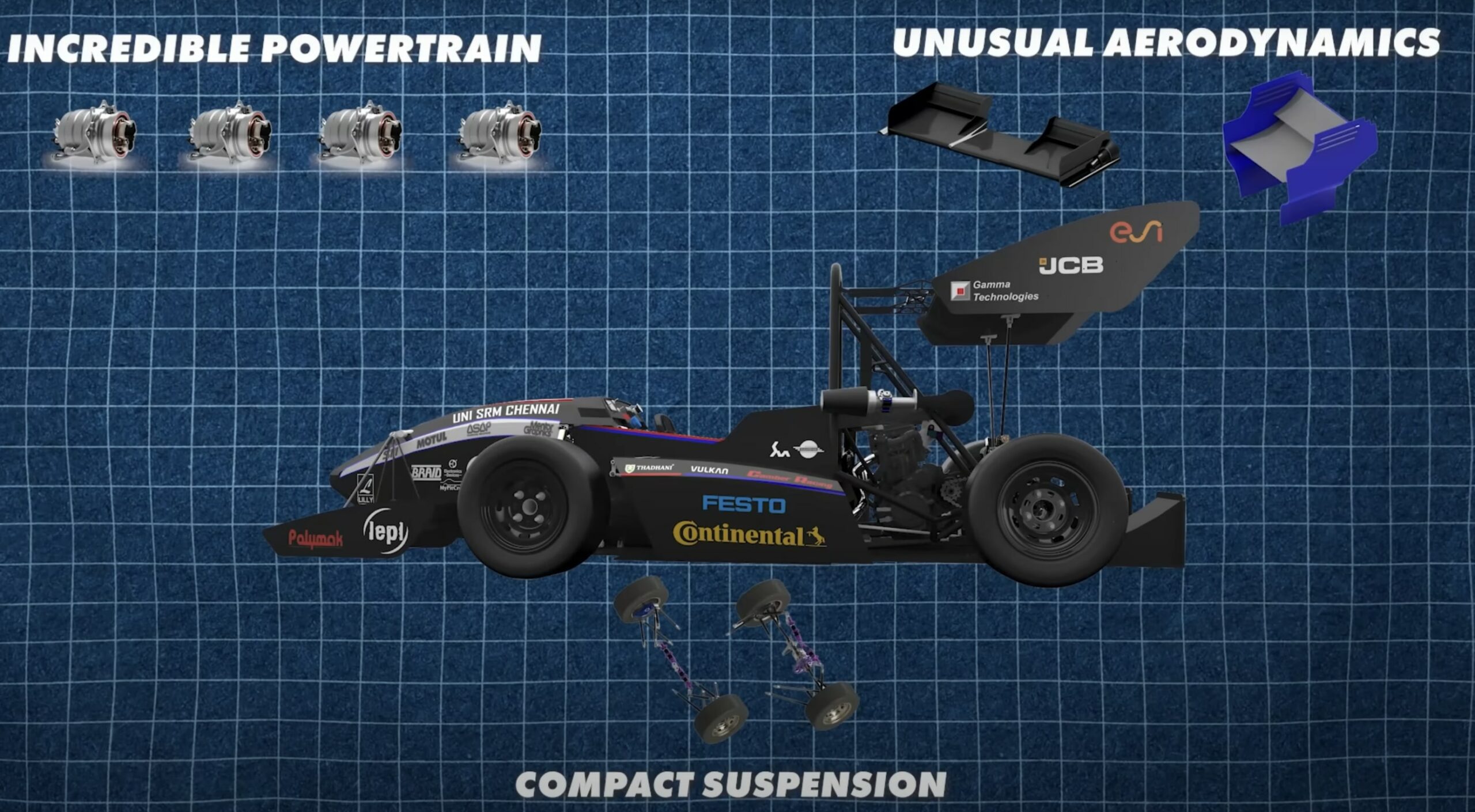
Advanced Aerodynamics
Like F1 cars, these student-built vehicles feature large wings for downforce, essential for maintaining traction through the winding Formula Student circuits. Teams work within regulated design dimensions to develop aerodynamics that maximise grip without focusing too much on reducing drag. The Oxford Brookes car, for instance, sports a large rear wing with a “swan neck” mount, improving downforce by keeping the lower surface of the wing smooth for airflow.
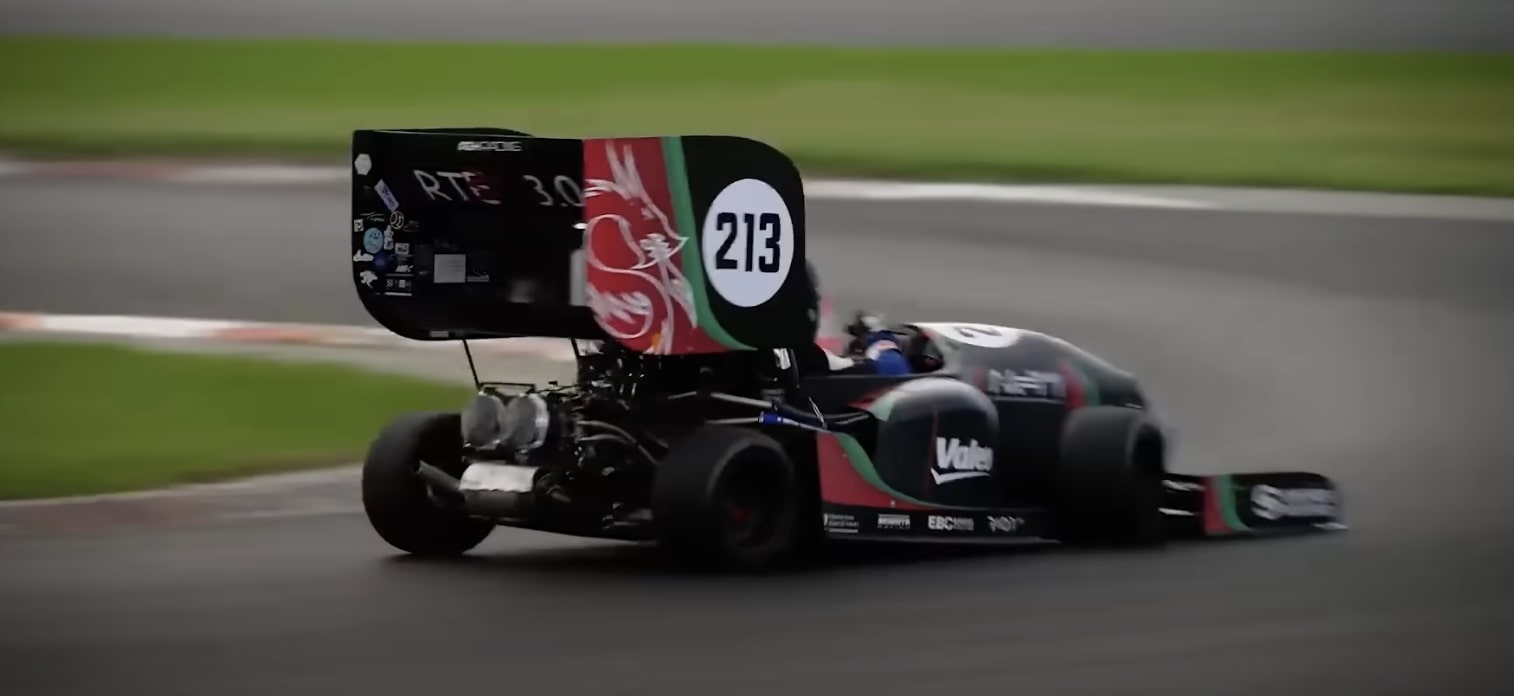
Regenerative Braking and Traction Control
The electric motors not only power the car but also serve as a regenerative braking system, converting braking energy back into battery charge. This system also doubles as a form of ABS, adjusting the torque to each wheel to prevent locking up. With both traction control and ABS-style braking, the car can handle wet conditions or uneven surfaces more effectively than a conventional vehicle.
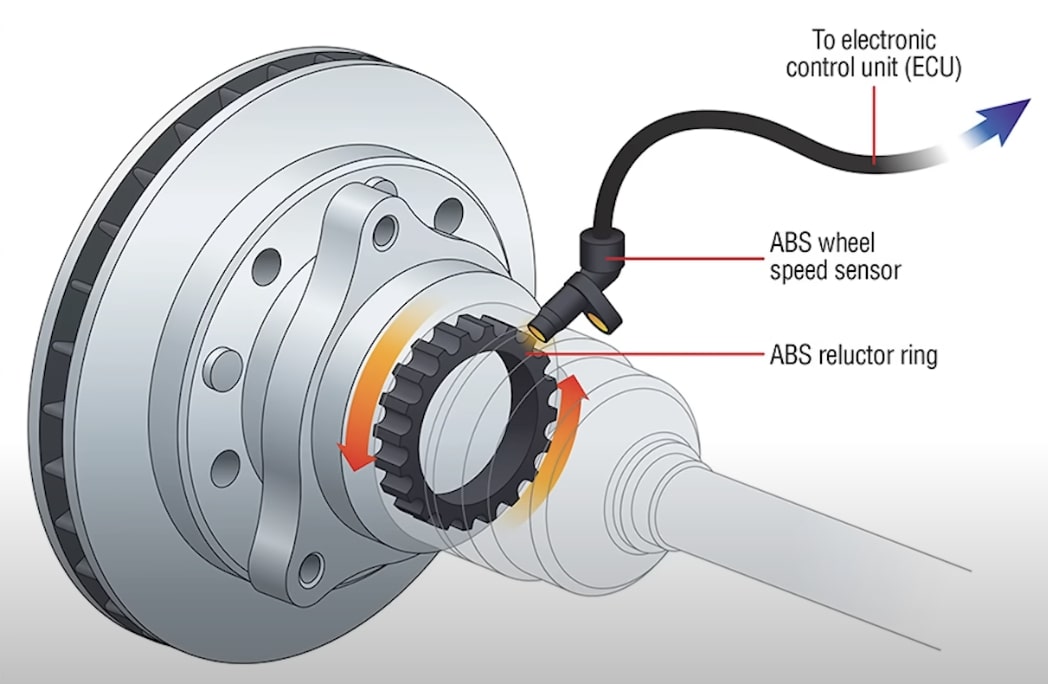
Precision Suspension and Handling
The car’s suspension uses a double wishbone, pushrod setup similar to that in F1. This lightweight, minimalistic approach ensures maximum contact between tires and track, crucial for handling on bumpy or twisty circuits. Suspension adjustments are further tested on a four-poster rig, simulating the car’s movements to fine-tune its grip and stability.
From Concept to Track-Ready
With an initial team of 80 students split into sub-teams, each working on a different aspect of the design, the team refines their ideas based on test results until they arrive at the final car design. Rather than using wind tunnels, the team relies on Computational Fluid Dynamics (CFD) to analyse aerodynamics, ensuring each component contributes to a cohesive aerodynamic package.
Formula Student exemplifies how academic motorsport projects are pushing the limits of what’s possible in engineering. These student-built cars demonstrate that innovation in motorsport isn’t just confined to F1 but is thriving in university workshops, where the next generation of engineers is preparing to take on the challenges of tomorrow’s racetracks.